Follow Brewer Science’s four tips on how to focus and organize your plate:
1. Know your strengths and use themWe are all much more productive when we are operating within our wheelhouse, doing those things that only we can do or that we can do best. Recognize what this is for you and aim for 80% of your time to be dedicated to this work.
In a manufacturing environment, it can be tempting to say that the regular users of the equipment are the people who know it best and should be the ones to perform regular preventative maintenance. Brewer Science used to do this, but, recognizing that this type of work is not the primary strength of the manufacturing technicians, the facilities team was brought in to complete preventative maintenance when needed. With a slight change in execution, this type of work gets done more efficiently and the manufacturing technicians can focus on their other duties that maximizes their strengths.
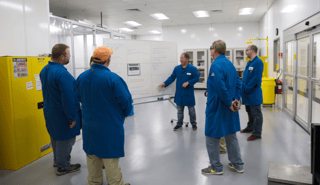
This will help keep what needs to be done in front of you and minimize the chances that something will fall through the cracks. As you look at what you’ve written, make sure it is clear and specific, has an associated deadline, and a realistic plan for achievement.
The Brewer Science manufacturing team uses the 5S approach and each work team keeps a 5S whiteboard posted in a prominent location where everyone sees it frequently during the work day. This keeps the goals, and plans for achieving them, front and center, and keeps the team focused on what is most important.
3. Know exactly what you need to work on a daily basis by using the ABCDE methodAs you look at your clearly written goals and plans, think about the following ABCDE method:
- A Items: Ask yourself, what absolutely must get done today? Once this is determined, these are your A items. In order to keep you focused, you should have no more than three A items each day.
- B items: These are items that should be done today but could slide a day or two without major consequences. Again, try not to have more than three to five each day.
- C items: These items would be nice to do, but, there are no negative consequences if you don’t get them done today.
- D items: Delegate, delegate, delegate. These are items that are in someone else’s wheelhouse and they will get them done much more efficiently than you or items that take you away from things in your wheelhouse and could be done just fine by someone else. These items can sometimes be tricky because these may be things that we enjoy doing but keep us from focusing on things that are more important.
- E items: Just eliminate E items as they are not related to achieving any of the goals and projects on your plate. Try to eliminate as many items as you can by asking yourself, “How does this get me where I need/want to be?”
The Brewer Science manufacturing team starts every morning with a huddle – right in front of the 5S board. Each work team identifies what has to be done that day. Everyone knows and understands what has to be done. In addition, knowing what is most important, the manufacturing team is reaching out to other teams within the company to evaluate work process and see if certain tasks should be moved or shared.
Manufacturing works closely with Material Handling and has delegated all responsibility for moving materials and finished goods to and from the production floor to our Material Handling personnel. Material Handling accesses the production schedule, can see the type of batches and when they are scheduled, and handles all arrangements for having the appropriate supplies ready to go as well as coordinating the movement of finished goods to storage and shipping.
4. Tackle the most difficult items firstWhat A or B item are you dreading? Our human nature would have us put that off until the end of the day, but, by tackling it and getting it done first, you ride the boost of successfully dealing with it the rest of the day – AND, it’s done!! Because, no matter how well we plan, things WILL pop up and threaten to derail our day.
If the pop up is an actual emergency, deal with it immediately and then get back to your planned day. If it’s not an emergency, ignore it for 30 minutes while you finish what you are doing. Then, and only then, figure out where it falls, assign it the appropriate letter (ABCDE) and move on.
In manufacturing, that perceived “emergency” might be something out of the ordinary in a batch of material. However, each material has a control plan with a response plan that technicians know to follow. So, the production supervisors don’t have to immediately react. They can finish what they are doing, making sure what must get done gets done. Then, once the control plan has been implemented, they can deal with it.
Achieve what you are capable of by following Brewer Science’s approach to focusing and prioritizing projects daily. You just might find yourself achieving more of the things you need and want to get done, rather than being swamped and too busy.
Take your manufacturing success to the next level by learning how Brewer Science amped up production volume and reduced waste through our Industry Week hosted webinar. Now available on-demand :: http://www.industryweek.com/webinar/CI-Deep-Dive.
Subscribe to Our Blog