What is Predictive Maintenance?
Tips on how to improve business efficiency with Predictive Maintenance
For businesses who seek to improve business efficiency by minimizing downtime and increasing productivity, predictive maintenance is where you will want to start. Predictive maintenance, also known as condition-based maintenance, is a proactive maintenance strategy that monitors the condition and performance of machines and tools in real-time to predict when they will need maintenance before it breaks down.
Using a combination of sensors, Internet of Things (IoT), machine learning, data analytics, and modeling, predictive maintenance will determine whether there are any warning signs for impending failure. This allows you to schedule maintenance when your equipment and machinery needs it, rather than merely guessing or waiting for a system failure, which could be detrimental for many industries, including potential for contamination of the line. If utilized frequently and correctly, predictive maintenance can help you avoid costly repairs and equipment downtime and could save your business money with increased efficiency.
Why is predictive maintenance helpful to businesses?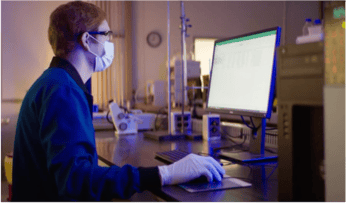
Since predictive maintenance is primarily executed by technological means (rather than manpower), it aims to increase efficiency and productivity, as well as to reduce maintenance and equipment costs for businesses over time. Predictive maintenance achieves this by predicting when maintenance is required, allowing the maintenance frequency to be as low as possible for an asset.
Predictive maintenance also proves to reduce unexpected breakdowns and machine downtime compared with more traditional methods of maintenance that involve manual inspections by a technician. In this sense, predictive maintenance might be viewed as a more advanced type of preventive maintenance, simply detecting faulty conditions more quickly and before equipment failure occurs.
What is the difference between predictive maintenance and preventive maintenance?
Predictive maintenance should not be confused with preventive maintenance, which is also a proactive maintenance strategy that has the same goal as predictive maintenance in preventing or minimizing the likelihood of equipment breakdowns. Preventive maintenance is primarily performed at the urging of time-sensitive triggers, such as weekly, monthly, or annually. It is also based on usage rate such as inspections taking place after every 1,000 hours of operation. Because preventive maintenance is done on a set schedule, it may lead to doing too much maintenance on equipment. Alternatively, predictive maintenance requires more advanced steps for accuracy and uses technology to assess when equipment requires maintenance. Some examples of technology used in predictive maintenance include:
- Condition-monitoring devices – Sensors are used to collect information on the performance of equipment. Depending on the type of sensor you used, information such as temperature, vibration, noise, and pressure can be collected.
- Internet of Things – IoT translates information collected by sensors such as temperature or vibration into digital signals that can be measured and analyzed over time to make predictions on when maintenance is required on the equipment.
- Machine learning – Machine learning uses the data generated from the sensors to learn the normal behavior of equipment and then when it has enough data, it can find anomalies in the performance of equipment. Machine learning depends on relevant and quality data to make accurate predictions.
- Computerized maintenance management system (CMMS) – A CMMS is crucial for the maintenance aspect of predictive maintenance; it creates a work order for a technician to complete when an anomaly occurs.
Condition-monitoring devices and a combination of these other predictive maintenance technologies may be used on any of your assets or machinery.
Another notable difference between preventive and predictive maintenance is the cost difference. Since preventive maintenance only involves labor costs, it's seemingly less expensive than predictive maintenance that requires a high initial capital investment on sensors, software, setup, and training.
Every business is different. Brewer Science offers specialized solutions based on the specific needs of the customer. Our in-house prototyping capabilities allow us to produce solutions fast and more affordable than our competitors.
How will predictive maintenance impact my business?
It will lead to increased efficiency and lowered costs. Naturally, every business is different, but using predictive maintenance for your most valuable equipment may yield significant return on investment. In fact, research provided by the U.S. Department of Energy shows that predictive maintenance could result in a 30%-40% savings for the business that implements it.
Machine downtime is expensive; you can avoid it with predictive maintenance. Many businesses suffer from unexpected downtime due to equipment malfunctions each year. Depending on the size of your business, downtime could cost you anywhere between $137 to $17,244 per minute! That is not including the potential of contamination in the case of a leaking or malfunctioning valve. Most business owners would want a crystal ball to predict the future of when to expect equipment malfunctions—and that’s essentially what predictive maintenance offers. By understanding the data, and making the necessary adjustments, you can save the business a significant amount of money, production time, and potentially paperwork. Predictive maintenance helps you plan for, and avoid, malfunctioning equipment that needs to be inspected or updated, so you can avoid downtime altogether.
Brewer Science combines materials science expertise, printed flexible electronics technology, and firmware development capabilities to deliver Flexible Hybrid Electronics (FHE) products that deliver actionable data required for today’s sophisticated IIoT environments. We offer a full range of electronics platforms, including sensors and systems, that are easily integrated into existing processes and products. Our complete end-to-end services range from small-scale prototyping and sensor manufacturing to user interface design, security protocols, as well as data-to-cloud capabilities. We can help you get your business started on the pathway of predictive maintenance. Visit our Smart Devices and PE Foundry page to learn more about the process or get in contact with an expert today to start your business process to optimization and automation.
Subscribe to Our Blog