The growing use of actionable information in new ways to make better decisions is driving brisk growth in printed electronics (PE) and sensors. According to BCC Research, the global market for sensors should grow from $173.4 billion in 2019 to reach $323.3 billion by 2024 – a compound annual growth rate (CAGR) of 13.3%.
Where will this growth come from? Where are the immediate, and longer-term, opportunities for companies with the skills and expertise to expand their presence in the sensor technology landscape? This article takes a look at these questions, providing some views from top innovators on the current and future state of the market, as well as what applications are the best fit for printed sensors. These experts presented their findings during “Next-Generation Sensing: Printed Sensors,” a workshop hosted by Brewer Science. Presentations from the workshop are available here.
Industry 4.0
Industry 4.0, or the Industrial Internet of Things (IIoT), refers to the growing trend toward automation and data exchange in manufacturing technologies and processes. This market, which is the sweet spot for many technology and materials providers, comprises several key aspects, e.g., the Internet of Things (IoT), cloud computing, and artificial intelligence (AI). In the Industry 4.0 ecosystem, machines communicate with the use of wireless connectivity and sensors to create smart manufacturing solutions.
What qualifies as a “thing” within the IIoT continues to expand, creating primary drivers behind new sensing technologies and solutions entering a growing number of Industry 4.0 markets. Key market segments for PE and sensors in this space include the following:
- Health care– This is where sensors have made the greatest inroads so far, thanks to fitness bands and other wearables, with many more opportunities pending.
- Transportation– Each new generation of vehicles integrates more and more sensors to capture and relay information to the driver, or to the autonomous car’s own “brain.”
- Environmental– Sensors play an increasingly valuable role in assessing weather and other environmental conditions and guiding controller systems to take appropriate action.
- Agricultural– Farms, both large and small, are recognizing the value sensors offer for such varied tasks as detecting humidity, regulating irrigation and measuring fields’ pH level.
- Warehousing– Sensors are becoming invaluable for tracking, monitoring and moving assets, as well as for controlling humidity, temperature, and other factors that can affect inventory.
Technologies
As Dr. Stefanie Harvey, R&D program manager for SEMI FlexTech and NanoBio Materials Consortium, notes, without the equipment and materials sector, none of the world’s leading consumer electronics companies would exist. The semiconductors, both rigid and flexible, that fuel their offerings must first be designed and validated, then fabricated using the optimal combination of equipment and materials, then packaged, assembled and tested, and finally integrated into the end-product during manufacture. As Figure 1 shows, it takes a cast of thousands to populate the ecosystem that makes up our emerging world of technologies and applications.
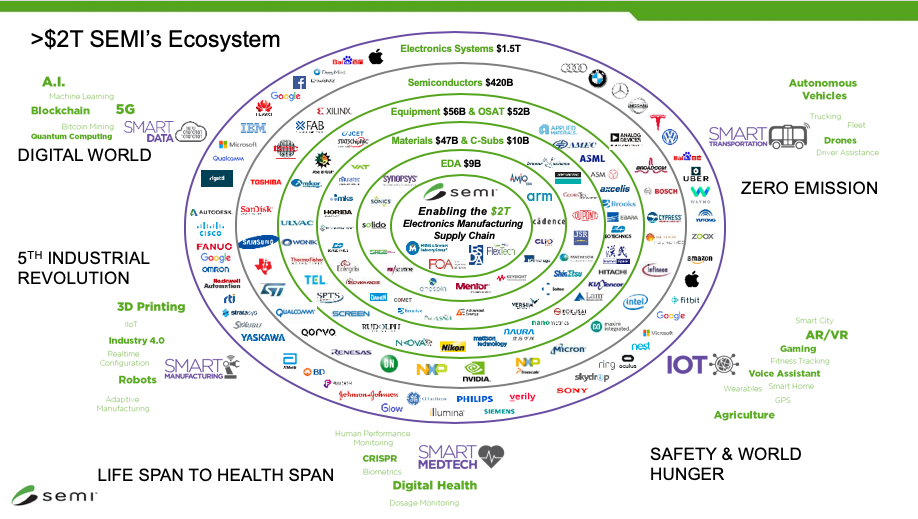
Figure 1. Industry association SEMI’s landscape of the greater electronics supply chain shows application verticals, many of which increasingly require flexible circuits/sensors.
Dr. Harvey further points out that technology evolution is greatly needed due to market timing and form factor/power requirements. Power is now the tricky piece for printed electronics – you can make the devices as small as possible, but because battery technology is not evolving quite as quickly, power remains a challenge.
Materials
Materials selection is an essential aspect of printed electronics design. Dr. Vijaya Kayastha presented on key materials requirements for flexible sensors. According to Dr. Kayastha, Brewer Science’s lead device development engineer, there are three main components for a basic printed temperature sensor/array: substrate, material, and encapsulant. Each has a number of parameters that must be considered when choosing which to use.
Substrate: As it is the largest component of the sensor, the choice of substrate – whether glass, metal or polymer – is vital, and comprises several desirable properties:
- Thermal robustness and stability
- Low moisture-vapor transmission rate (MVTR)
- Inertness to other conditions, e.g., humidity, volatile organic compounds (VOCs), gases, etc.
- Excellent thermal conductivity
- No outgassing
Differing performance between substrates is caused by differences in glass temperature, thermal stability and degradation, and high-temperature inertness.
Sensing material: The choice of sensing material, e.g., printed silver or sputtered gold, is also dependent on a set of desired properties:
- Larger response to temperature change (temperature coefficient of resistance, or TCR)
- Temperature response linearity
- Thermal robustness / lack of degradation
- Repeatability over a wide range of temperatures
- Inertness to other conditions, e.g., humidity, VOCs, gases, bending
- Excellent thermal conductivity
Performance differences between sensing materials are typically caused by differing TCRs, residual solvents in printed films, contact resistance, and how they respond to other conditions.
Encapsulant: Encapsulation is required for protecting the active elements on the electronic device from degradation when exposed to moisture and oxygen. Thus, choosing the right encapsulant material (typically, some type of barrier film) is essential to preventing loss of device performance. Desired encapsulant properties include:
- Thermal robustness
- Stability across a wide temperature range
- Good adhesion to the substrate and active layer
- Good barrier against environmental conditions such as humidity, VOCs, gases, etc.
- Excellent thermal conductivity
Causes of differing performance between encapsulant materials include difference in material thermal properties (Tg, thermal expansion, stability), different solvents and incomplete curing, or mismatched thermal expansion between the substrate and active layer.
Sensor types
Choice of materials also hinges on the type of sensor to be manufactured. One of the most fundamental is temperature sensors.
Temperature
Temperature measurement is vital to Industry 4.0 applications – not to mention smart buildings, automotive, military and aerospace… virtually any environment (Figure 2). As this function has become more sophisticated, it requires more streamlined solutions that are easier to implement.
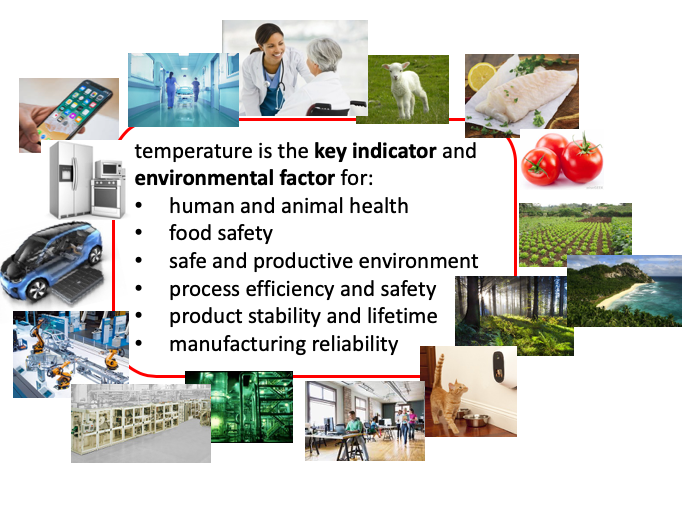
Figure 2. Accurate, flexible temperature measurement and monitoring is essential to our overall welfare. [Source: PST Sensors]
Because temperature measurement is so crucial, Margit Harding, CEO of PST Sensors, has coined the term “Internet of Temperature” for IoT, noting that, “as the most often measured physical quantity, temperature measurement is needed anywhere and everywhere.” There are a number of different types of sensors for measuring temperature, and companies in this space have found that some are better suited than others to flexible applications.
PST Sensors, for example, focuses on printed thermistors – thermally sensitive resistors whose resistance changes exponentially in conjunction with temperature variations – which the company makes by taking actual silicon, breaking it up into very fine pieces, and then printing. The goal is to enable state-of-the-art sensing that goes beyond conventional requirements. As the company notes, in the era of IoT (in both senses), no longer does the traditional control loop of comparing single sequential and data and performing a single action apply. Today, correlated sets of data can be compared, and multiple actions performed, thanks to the IoT and printed sensor electronics.
Brewer Science sees this fact as making a strong case for temperature sensor arrays, which the company offers as flexible hybrid electronic (FHE) systems – ideal for measuring temperature in confined spaces with narrow areas, where typical silicon sensors can’t fit. FHE arrays are key for measuring multi-point surface temperature. The company’s sensors are based on resistive temperature detection (RTD) technology, which measure temperature by passing a low-level current through electrodes and measuring voltage drop across them.
Moisture
Printed sensors that can measure and monitor moisture levels are another application of growing importance for Industry 4.0. One example is the carbon-based, resistive-type sensors offered by Brewer Science, which respond to fluctuations in humidity within 10 ms, operate at very low power, and can be printed on any surface. The sensors can be integrated with many commercial devices, including slow (but accurate) existing moisture sensors, to achieve high speed and accuracy in a single sensor system.
In each of the key market areas described earlier, excessive or too little moisture can have a detrimental effect – certainly, ag-tech is a prime candidate for moisture sensors, given the sensitive nature of crop-raising. Dr. Nadia Shakoor, senior research scientist with the Donald Danforth Plant Science Center, notes that printed sensors have many applications in this area (see Figure 3).
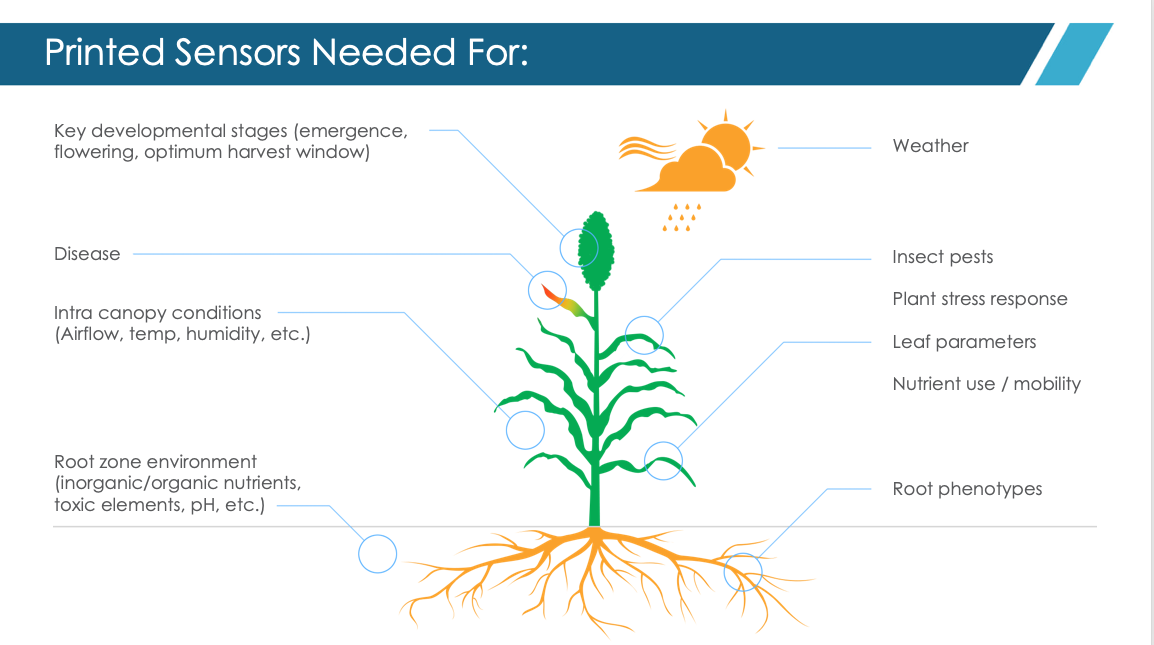
Figure 3. Printed sensors have great application potential for measuring and monitoring a range of vital parameters related to plant and crop technology. [Source: Danforth]
Dr. Shakoor confirms that the future of successful farming and breeding operations will rely heavily on sensor technology. She further notes that sensors must have all the following capabilities in order to be viable for agricultural applications:
- Scalable
- Biodegradable/easily removed
- Low cost
- Durable/weather-resistant
- ow power
- Connected (WiFi, cellular 4G/5G, LoRaWAN, etc.)
- Use standard communication protocols
- Function as edge sensors/devices
Future smart farms will use sensors extensively, including being powered by sustainable energy, with many functions automated to enable farmers and engineers to focus on optimizing the operation.
Dealing with drift
While printed sensors offer many advantages for a range of applications, one challenge that can create problems with accuracy is sensor drift, which is caused by the sensor’s less rigid, more flexible structure. A common problem that can lead to inaccurate temperature measurement readings, sensor drift can be caused by environmental contamination, vibration or extreme temperature fluctuations – essentially temperature readings may vary across the surface of the sensor.
Enhanced performance from printed sensors can be achieved through the proper choice of substrate, sensor material, and manufacturing process. Printed temperature sensors have achieved accuracy of 0.5°C in the –20°C to 100°C range and drift (100°C/100 days) of <2.0°C. As printed sensor use broadens and manufacturers tweak their products to accommodate customers feedback and requirements, these numbers will only improve.
Electronics
One way that PE technologies will grow in capability and value is by looking at use cases and ensuring that they are not taking a one-size-fits-all approach to different markets – particularly when it comes to developing solutions for consumer vs. industrial applications. They must be adjusted to fit the individual market needs.
Dean Hotvet, director of printed electronics at Xymox Technologies, makes this point very succinctly, noting that technology for its own sake is not the best approach to any application. To be successful in their implementation, sensors require three key factors:
1) Efficiency – consumer and industrial applications are rarely interchangeable because the markets have different needs, and the “field of dreams” mentality rarely works when introducing new products to the consumer sector. If you’re not making thing more efficient or solving a problem, your sensor product won’t gain a foothold.
2) True need – sensors require electronics, but customers care more about complete solutions than novel materials, particularly in the consumer sector. It’s vital to ensure you’re supplying what the customer really needs, not just a portion. For example, you can design a smartphone with the most updated, futuristic look on the market, but if it doesn’t have touch capability, users won’t be interested.
3) Ecosystem – the customer’s and supplier’s ecosystems are not always aligned. Looking again at the touchscreen example, an industrial-device manufacturer’s requirements may be out of sync with an ecosystem geared for touchscreen inputs based on consumer products. There are a number of factors that differ between the two – end-user experience, design cycles, supply-chain issues, and when products are “end-of-lifed.” Sensor makers and their customers must be operating on the same principles to ensure stakeholders’ needs are met.
Partnerships
Creating effective ecosystems requires cooperation and open dialogue between customers and suppliers. This includes companies that may have some competitive technologies, such as Brewer Science and PST, talking together in open venues with the shared goal of helping to improve the technology and advance the market.
This is one important function of organizations like SEMI/FlexTech Alliance and NextFlex. They help connect developers, suppliers and manufacturers so that they can work together on new solutions and mutually beneficial opportunities. Because these associations also focus on building public-private partnerships involving academia, governments and non-profits, they can be built in parallel with corporate partnerships.
The bottom line is that the printed electronics sensor market will continue to grow, with the support and cooperation of all those invested in making it a success.
Subscribe to Our Blog